В предыдущей статье я пообещал продолжить свой рассказ про моё внезапное путешествие в Москву по приглашению компании Энергоконтракт. Обещание сдерживаю, публикую отзыв про экскурсию на собственное производство специальной термостойкой одежды Энергоконтракта.
Напоминаю, что вся одежда, которую производит Энергоконтракт – действительно собственного производства, только обувь и некоторые средства индивидуальной защиты вроде очков и касок – на аутсорсинге. А всё сырьё – от проверенных временем и стихиями фирм Dupont, Uvex, 3M.
Полностью эмоции, которые были у меня, передать не получится – ведь я не писатель-романист. Но могу сказать в общем вот что.
Уважаю фирмы, в которых чётко отлажен производственный процесс, начиная от разработки дизайна и закупки сырья до упаковки и отгрузки готовой продукции. Меня восхищает то, как работают большие успешные фирмы. По себе знаю, как тяжело самоорганизоваться, а организовать производство с большим количеством людей гораздо сложнее.
Недавно видел документальный фильм, как производят автомобили BMV в Германии. Могу сказать, что на производстве Энергоконтракта многое достигнуто, но стремиться ещё есть к чему ;)
Но начнём по порядку.
Содержание статьи:
Поездка в Томилино
Томилино – пригород Москвы, в районе Люберец. Москва большая, ехали мы через центр, больше часа, пришлось постоять в знаменитых московских пробках. Тем не менее, в окно я почти не смотрел. То, что происходило в нашем автобусе, было гораздо интереснее. Мы знакомились, рассказывали о своей деятельности, делились впечатлениями, случаями из жизни.
Мария, PR-менеджер, интересный рассказчик, много рассказала интересного о компании, о клиентах, о случаях на производстве.
Например, всем понравился рассказ про энергетика, который на природе по известным причинам уснул, а рукав его термостойкого свитера оказался в костре. И никаких ожогов, хотя свитер конечно стал уже не таким элегантным. После этого все ещё долго шутили на этот счёт: “О, а вот в таких свитерах можно спать в костре?”
Наконец, мы приехали в производственный корпус Энергоконтракта:
На проходной висит такая карта с лейблами (нашивками). И это – далеко не все клиенты, а только те, что поместились:
Далее состоялась экскурсия по цехам, тут для меня была самая интересная часть поездки.
Цех обработки ткани
Термостойкая ткань имеет свои особенности по обработке, поэтому её обрабатывают по особым технологиям с использованием специального оборудования. Оборудование итальянское, новое, проектировалось специально под данное производство, с учетом специфики.
Суровая (от слова “сырая”, как сырьё) ткань поступает на предприятие в рулонах. Сначала она проверяется на брак и соответствие характеристикам на специальной машине. Затем обычную ткань красят. Тут очень сложная и ответственная часть тех.процесса, ведь термостойкая ткань должна быть покрашена качественной термостойкой краской.
Краска эта должна выдержать жёсткие условия эксплуатации, множество стирок, и при этом не должна блекнуть.
Для покраски ткани используется специальная машина – высокотемпературный джиггер. Говорят, таких джиггеров в России больше нет.
Через верхний ролик ткань загружается, и “варится” в джиггере несколько часов.
Конкуренты Энергоконтракта используют для спецодежды готовые, покрашенные ткани, либо используют не столь совершенные методы окраски.
Окраска – это грязное производство, и в том же цеху стоят компактные очистные сооружения, которые чистят технологическую воду, в результате стоки соответствуют норме.
Раскройный цех
В раскройном цеху ткань кроится на детали одежды, из которых в швейном цеху сшиваются уже готовые куртки, брюки, и другая одежда.
Я работал на обувном производстве, там для этих целей используют вырубные пресса, например как этот. Конечно, это середина прошлого века.
На производстве Энергоконтракта используют раскройные машины, в основе которых – компьютерное управление и компьютерный расчёт. В результате детали кроятся таким оптимальным образом, что отходов остаётся очень мало.
А отходы поступают на специальную машину, которая распушивает кусочки ткани до состояния материала, который идёт на утепляющий слой в зимних куртках. Этот слой, логично, тоже получается термостойкий.
Швейный цех
Из раскройного цеха детали поступают с сборочный цех, где собственно и происходит главное – получается готовая одежда.
Швейный цех поразил меня своими размерами – одновременно в нём трудится более 150 человек. Швейные машинки более 90% – японские Juki, есть несколько немецких Pfaff и несколько специализированных машин, например эта:
Такая машинка по шаблону из кусочка ткани изготавливает сложные для ручной обработки детали – например, карманы, воротники.
Процесс сборки зимней куртки сложен, требует особой сноровки и терпения, вот на фото куртку из нескольких слоёв собирают два человека:
А вот в швейном цеху висела готовая форма для энергетиков, обслуживающих высоковольтные линии ОАО РЖД:
Другой вариант готовой спецодежды – на фото в начале статьи.
Перемещаемся дальше.
Трикотажный цех
В этом цеху изготавливается то, что нужно одевать под верхнюю одежду – подшлемники, рубахи, свитера, перчатки, и т.д.
Всё делается из термостойкой ткани. Это ткань ничуть не хуже обычной качественной ткани, прекрасно подходит к телу, мягкая и прочная.
Меня поразили некоторые машины, о существовании которых я даже не догадывался. Например, машина для вязания горла для свитера. Свитера сшиваются из готовых деталей с помощью термостойкой нити.
Те самые свитера, в которых можно спать в костре :)
В сторонке стояло несколько станочков, которые жужжали без участия человека – а из них падали перчатки!
Цех текстильной печати
На производстве Энергоконтракта есть цех, где методом шелкографии производят нашивки на спецодежду. Конечно, нашивки эти тоже термостойкие и особо прочные. В результате спецодежда становится “брендовой”.
В цеху основной станок – карусель, в которой по шаблонам наносится рисунок. Большинство процессов автоматизированы, операторы только загружают заготовки и принимают готовую продукцию.
Мне довелось поработать на ручной карусели, которая использовалась раньше, а сейчас работает только на малых заказах. Краска наносится в ручную, пластиковым шпателем, продавливается через тончайшую сетку, и печатается на ткани. Затем поступает в туннельную печь, где происходит вулканизация.
Вот такую нашивку я сделал своими руками, с гордостью показал её своим родным по приезду:
Вспомнилось, как в садике делал разные поделки – типа аппликаций на ткани.
Вот пример нашивки-информера, я писал о таких в конце первой части.
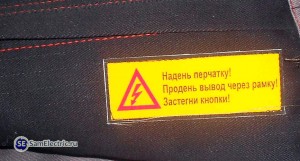
Предупреждения. Для полной безопасности и эффективности термостойкой одежды надо строго следовать инструкциям по её применению.
Экспериментальное производство
Название цеха говорит само за себя – здесь делают штучный товар. Получают техническое задание от заказчика, и делают компьютерный дизайн прототипа. Затем вручную выкраивают детали одежды, и сшивают, получая, например, брюки в единственном экземпляре. Эти брюки проходят строгие испытания по всем параметрам, включая удобство, качество кроя, оптимальность для потокового производства.
По удобству надо сказать отдельно. Важно, что о трудовом человеке заботятся, продумывая каждую мелочь в его одежде. Ведь часто приходится работать и с высоко поднятыми руками, и на присядках, и на карачках на корточках.
Например, в обычных брюках перед тем, как присесть, приходится руками поднимать штанины. В брюках, разработанных в опытном цеху Энергоконтракта, эта мелочь продумана, конструкция такая, что человек думает только о работе.
Далее был обед в рабочей столовой – самая вкусная часть экскурсии, но не будем отвлекаться.
Лаборатория испытаний СИЗ
После обеда мы поехали в испытательный центр “ИнтерСИЗ”.
Чтобы проверить качество средств индивидуальной защиты, нужно измерить некоторые параметры. А чтобы их измерить, нужна методика испытаний и специальное сертифицированное оборудование.
Всё это в лаборатории есть. Вкратце опишу, что мы там видели.
Испытание ткани на горючесть
В специальной установке кусочек подопытной ткани подвергается действию газовой горелки. Вот мы поджигали термостойкую ткань Номекс в течении 5 секунд:
Могу заверить, что ткань прекратила гореть даже раньше, чем прекратилось пламя. Да и горением это трудно назвать, просто пламя взбиралось по ткани, а ткань карбонизировалась.
Зато обычная ткань горела отлично, распавшись в конце на два обугленных кусочка:
Испытание прочности на разрыв
Специальная установка разрывает полоску ткани, при этом данные поступают на компьютер, процесс видно в динамике:
Фотоаппарат у меня похуже, чем на этом фото, однако выложу фото экрана компьютера за секунду до разрыва, где видно, что ткань выдержала почти 1300 Ньютонов, или 130 кг:
Проверка смачиваемости
Тут науки не очень много, поскольку наука начинается там, где начинаются измерения. Оценивается смачиваемость субъективно, на вот такой установке:
Ткань смачивается водой, а потом – каплями нефти.
Интересно, что купить сырую нефть в малых количествах (10-20 кг) крайне проблематично. Поэтому сертифицированную нефть доставали окольными путями, через партнеров (клиентов) Энергоконтракта.
Установка для проверки прочности обуви
В рабочей обуви (фото моих любимых ботинок Uvex я выложил в первой части) особо прочный подносок из металла. Это сделано для предотвращения травм ступней, особо частых на производстве.
Однажды я сам опустил себе на ногу рохлю (гидравлическая ручная тележка)!!!. Пожалел, что тогда не было спецобуви – был в обычных туфлях)))
В установке груз определённой массы сбрасывается с высоты 1 метр на носок ботинка. А в ботинке установлен столбик пластилина. По деформации пластилина определяется прочность носка.
Окончание экскурсии
Многое хотелось рассказать, но это просто физически невозможно. Время пролетело очень быстро и насыщенно.
И вот – я лечу домой:
Александр молодец, что выкладывает фото экскурсий на завод, это всегда интересно. Как правило в проходной заводов висит табличка фото-видеосъёмка запрещена. Когда принимал БКТП 2х1600 в Чебоксарах – ЧЭАЗ , настоял, что глазами всё не охвачу, разрешили втихушку фотографировать. Вечером в гостинице на фото увидел, что фидерные автоматы не тех. номиналов. В Узэектроаппарате (Ташкент) в проходной изъяли фотоаппарат, при выходе вернули.
Да, тут охрана бдит. Например, когда я был на производстве в Германии, получал разрешение на фотографирование только на строго определённое оборудование.
А на Энергоконтракте всё было можно, некоторые блоггеры одновременно делали фото, снимали видео, и писали на диктофон.
Сейчас, через два года, понимаю – главное в этой поездке – это знакомства и навыки общения, которые я приобрёл.
На втором месте – организация производства.